- Manufacturing Industries
- Sensors & Cameras
Troldtekt
Troldtekt is a Danish provider of sustainable acoustic solutions. Since 1935, Troldtekt has been designing, developing and producing cement-bonded wood wool panels in Denmark, which are sold in a number of countries around the world. Troldtekt addresses a broad target group due to its far-reaching applicability of the acoustic panels, which can clad ceilings and walls in most types of buildings, e.g. in private homes, offices, commercial and industrial buildings as well as in public buildings, such as educational institutions, hotels, restaurants, cultural and sports centres.
130 employees are dispersed among the headquarter and the modern production facilities in Denmark, and two internationally situated administrative centers. The acoustic panels are produced from 100% natural and local materials and the final product resembles an intelligent acoustic solution that offers a meaningful combination of inspiring architecture, high-quality sound environments and a sustainable indoor climate.
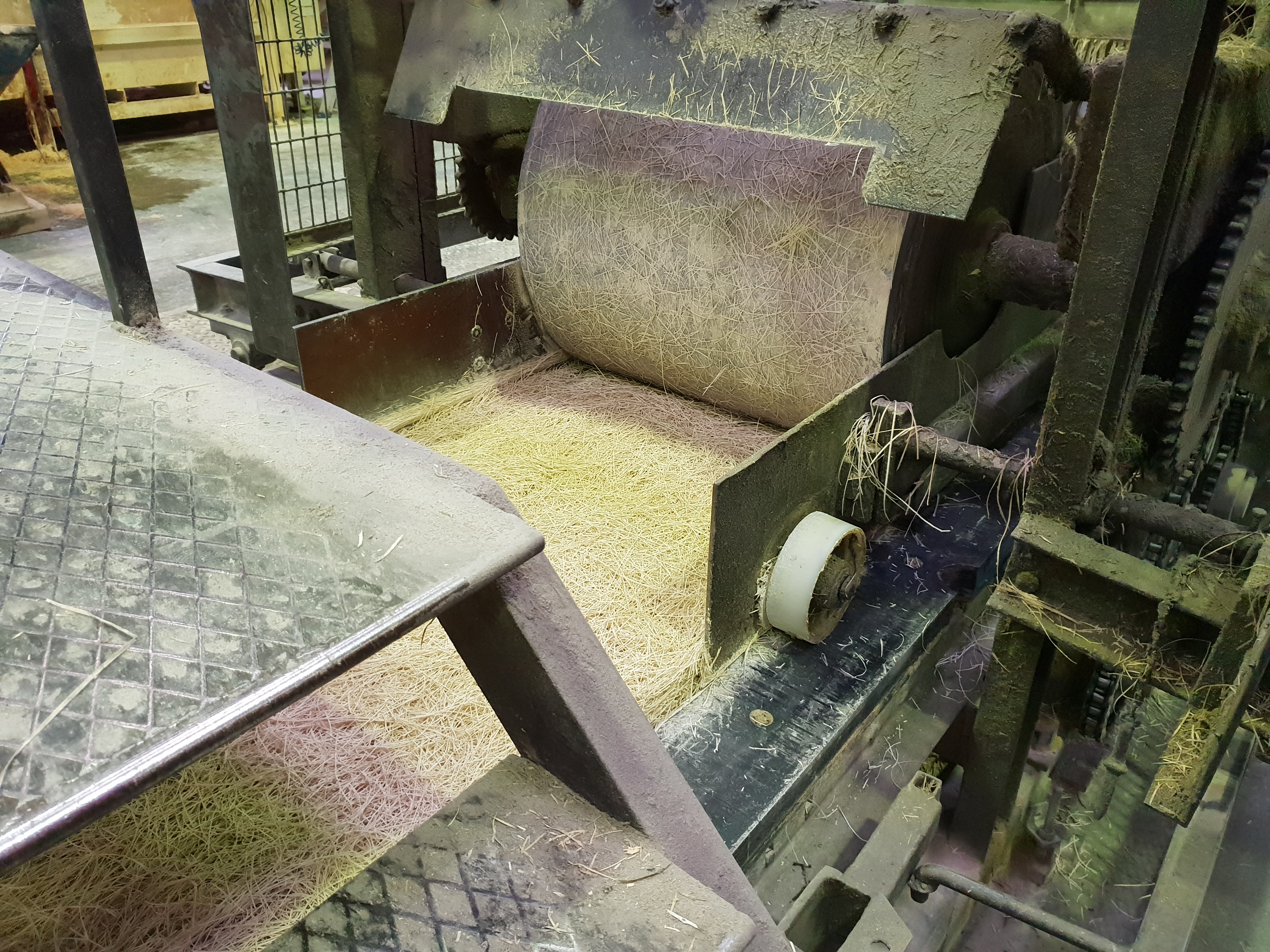
Illustration 1: A mixture of wood wool, cement and water is distributed evenly in moulds to achieve a uniform appearance prior to the first quality control
Today, the acoustic panels are among the leading and preferred solutions for ensuring high-quality sound environments. The vision of Troldtekt is to be a trendsetter within intelligent acoustic solutions with focus on a sustainable indoor climate. This is pursued throughout the entire product life cycle – from cradle to cradle, in materials, production, transport, use and recycling. In this context, Troldtekt focuses on minimising its environmental impact by optimising processes and resource consumption.
Open and download appendix: About Troldtekt elaborated.
IoT incentive
Accurate moisture content in Troldtekt’s acoustic panels is a crucial factor for the quality of the final product. When products are not approved in the company’s stringent quality control, they are deemed defective and demolished. Meanwhile, moisture levels are difficult to measure and control, as regulation is navigated by manual machine configurations in the production line. Consequently, Troldtekt had a desire to make more objectively informed decisions about these configurations and production operations in general. At that time, operational decision making was driven by ‘gut feeling’ and intuition of the operators, which would cause less than optimal machine and process performance, and ultimately result in a recurrently severe product defect rate, and thus, substantial costs due to demolition and waste.
“Looking some years ahead, we see that our biggest challenge will be that the company growth and turnover rate will be dependent on how digitally mature we are.”
Peer Leth, CEO at Troldtekt
Troldtekt began collecting data from the embedded PLCs[1] of the production machines to gain an insight into how various operating factors and manual configurations affected product quality. However, the diversity of the data systems encoded by the machine suppliers made it difficult for Troldtekt to consolidate information, and the insights to respond to this knowledge therefore remained absent.
In 2019, Troldtekt gained awareness of an Industry 4.0 enablement project, aiming to boost digital maturity in industrial environments. The project was contemplated by DBD and PulseLabs, and funded by the DIATOMIC research initiative, aiming to propel manufacturing companies in the right direction to benefit from IIoT technologies. Troldtekt’s choice of the specific IoT solution was underpinned the collaborative effort between the company and the team of IoT specialists represented by the project, whom worked collectively to identify IoT empowered solutions for the extant operational challenges experienced by Troldtekt.
The IoT solution
The core hardware component of the IIoT[2] project was a simple technology: a wireless PLC sensor in a plug and play format, which could be moved around in Troldtekt’s production and was compatible with all types of machinery.
Open and download appendix: Wireless PLC sensor.
Illustration 2: Wireless PLC sensor
The final solution included a microservice, using MQTT[3] and a NoSQL[4] database to integrate the different sources of production data for retrieval and presentation in the hybrid web app. This supported the back-office IT with better ways to extract additional telemetric data from the already existing PLCs, all of which had to be merged and correlated, ultimately enabling Troldtekt to leverage production data to improve operational performance and identify optimisation potentials.
Illustration 3: Defect tracking buttons
The IIoT project was broken up into three iterations, each advancing the technological capability of Troldtekt’s production process and each based on learnings from the previous one. An overview of the iterations is provided below.
Open and download appendix: The Troldtekt production process.
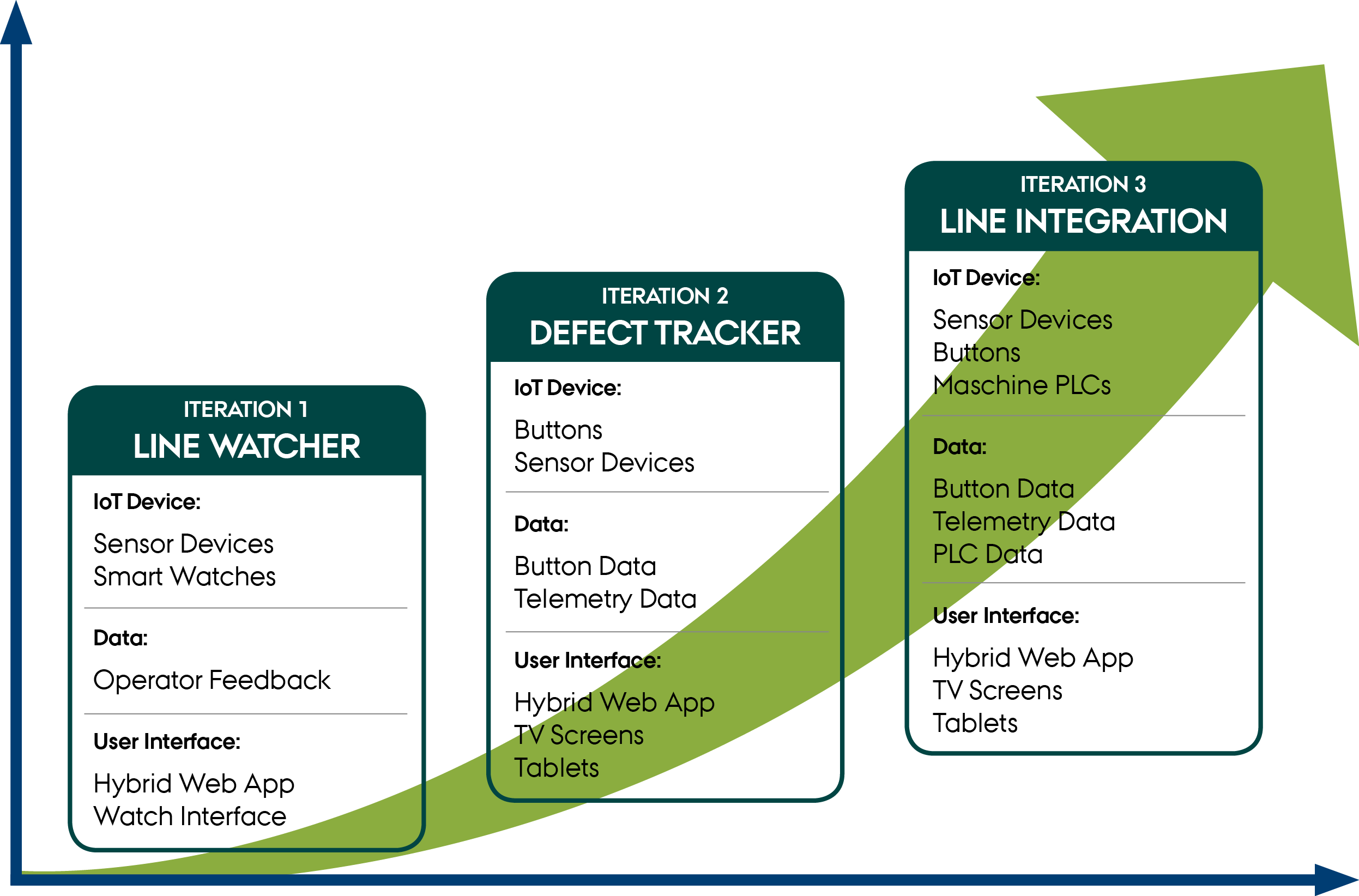
Illustration 4: The concept of the IIoT iterations relied on three key elements: an IoT device, a user interface and the data between those two elements
Outcome of the IoT solution
The implemented IoT solution has allowed Troldtekt to merge data across machines, production environment and manual configurations, enabling consistent analysis and correlation of operations to provide insights into the overall performance of the production. The profound ability to leverage data has facilitated prescriptive knowledge of daily operations, which has transformed the company’s production into an increasingly data-driven venture. This transition has in particular effected two major outcomes:
- Data-driven decision making: Extracting correlations and facts from data to make inferences that provide guidance for making decisions and taking operational actions.
“A main learning is really to accept that data is a needed platform for decision making.”
Peer Leth, CEO at Troldtekt
- Quality management: Identifying influencing factors that are less than optimal for specific operations, procedures or processes, enabling a reduction in previously untraceable defects and regulating environmental conditions to support excellent quality.
“It has given us a better platform for our quality management system and for knowing about our quality – not just when we are manufacturing good or bad quality – but also why.”
Peer Leth, CEO at Troldtekt
Hence, the impact of implementing the IoT solution has been noticeable at organisational level at Troldtekt, and seemingly at the level of individuals as well. Production operators have gained a comprehensive understanding of the overall impact of the specific quality processes and machine configurations for which they are responsible. Production managers are now able to analyse abstract machine data for trend identification and operations forecasting, enabling defect detection and recipe improvements. The technical team has gained objective insights into process changes and machine configurations, which have enabled databased maintenance and improved collaboration with machine suppliers. Finally, the management team has gained valuable data insights that can be used when approaching new international partners and customers as well as for strategic decisions.
Best practice learnings
A curious openness and an agile mind-set have been vital attitudinal practices along the process of IoT implementation, aiding Troldtekt to translate a range of problematic encounters into a range of cross-functional learning experiences. These learnings pertained both technically, organisationally and businesswise, and ultimately, they map out the steps taken on Troldtekt’s road to successful implementation. This include the value found in small-scale iterative development, collaborations across the ecosystem as well as the matrix use of data, technology and know-how. Likewise, the importance of continuous evaluation, involvement of the right people and strong communication throughout the organisation.
“It is really important to have a clear and direct communication to employees about this journey and that it has just started. The level will only increase in the future…”
Peer Leth, CEO at Troldtekt
Another vital factor of success is the genuine belief that digitalisation and IoT is ordained to shape the future business of Troldtekt, and that prospects of the implemented solution go beyond the immediate outcome, nurturing further potential for the company to derive from leveraging production data.
“We expect to become even more focused on data.”
Peer Leth, CEO at Troldtekt
Specific prospects include:
- Facility management: Potential for learning and pre-programming the optimal conditions leading to automated machine configurations, and thus prolonged equipment lifespan and enriched product quality.
- Asset management: Potential data integration with partners allowing tracking of product location, status and condition throughout the entire value chain for better management of resources and assets (upstream and downstream).
- Predictive maintenance: Potential to not only track machine performance, but also to predict deviations even before they occur, enabling preventive action before a product component part fails or a machine stops and/or breaks down.
Looking to the future, the significance of IoT at Troldtekt is considered increasingly impactful with its progressive potential to reduce costs and the environmental impact as well as increase revenue.
“I’m sure, when looking two years ahead, we will be a completely different company.”
Peer Leth, CEO at Troldtekt
Digital maturity of Troldtekt
Illustration 5: Digital Maturity Radar Chart: Assessment of Troldtekt by Peer Leth, CEO
Troldtekt assumes a high level of digital maturity with an overall score of 3.73. The score indicates that the digital capabilities of the company are relatively mature, and that they perform above average for the sector.
The Digital Maturity Assessment Tool is copyrighted by Associate Professor and PhD Annabeth Aagaard, Director at the Interdisciplinary Centre for Digital Business Development, Aarhus University. To get the digital maturity of your company mapped out, click here.
End notes
[1] PLC (Programmable logic controllers): Miniature industrial computers that contain hardware and software used to perform control functions.
[2] IIoT (Industrial Internet of Things): The use of smart sensors and actuators to enhance manufacturing and industrial processes.
[3] MQTT: An OASIS standard messaging protocol for the Internet of Things (IoT).
[4] NoSQL (Non-relational data base): A database that provides a mechanism for storage and retrieval of data.
Copyright notice: © 2020 – 2023 EU-IoT Consortium.
This material was produced as part of the EU-IoT project, grant ID 956671, and is funded by the Horizon 2020 Framework Programme under topic ID ICT-56-2020.
EU-IoT is the European IoT Hub. The EU-IoT project works towards growing a sustainable and comprehensive ecosystem for Next Generation Internet of Things.
Source of origin: Information to document this use case originates from the H2020 call: ICT-04-2017 Smart Anything Everywhere Initiative (IA); Project DIATOMIC 761809; Period: 01-19-2017 to 31-08-2020; EC contribution 8 mil. EUR.